Kombinierte Ziehsysteme
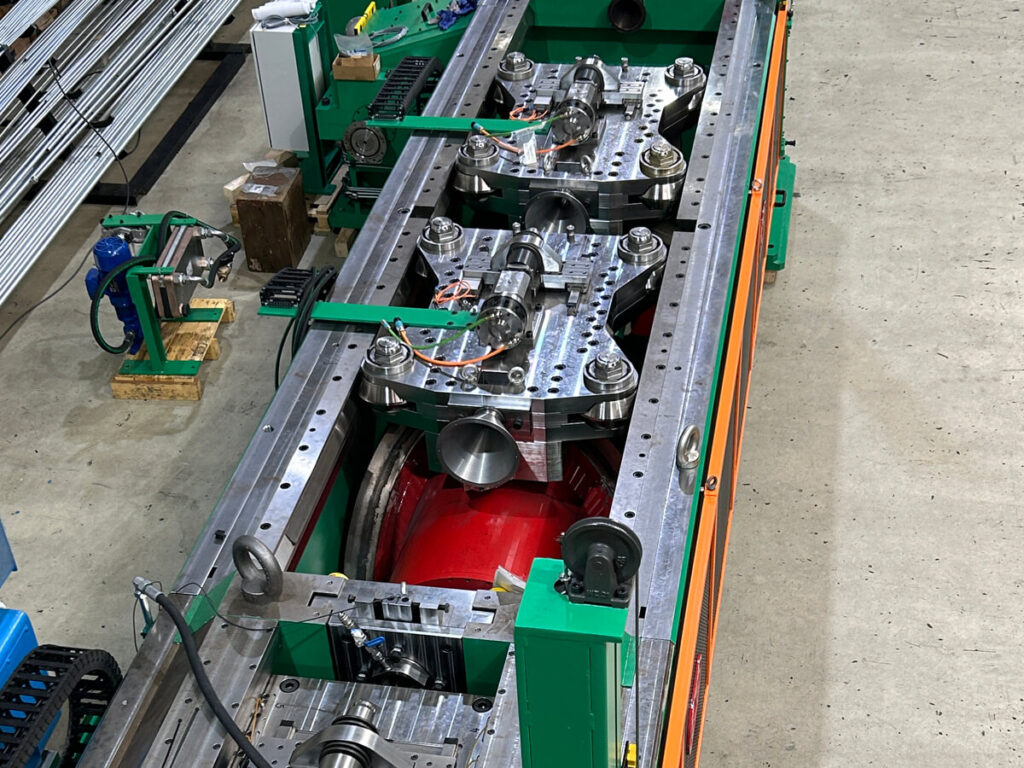
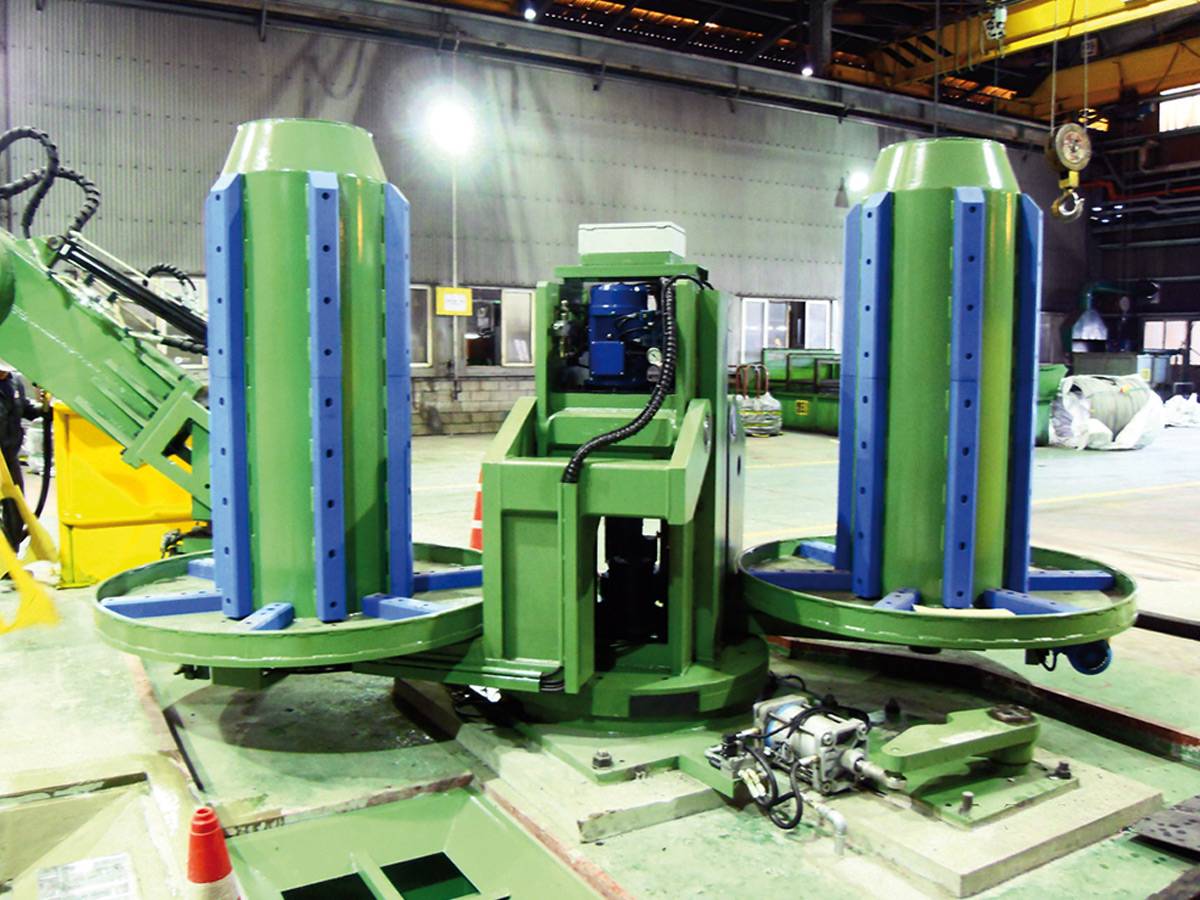
Doppelhaspel
Die Doppelhaspel sorgt für die schnellere Zuführung des Ausgangsmaterials. Jede der beiden Kronen kann während des laufenden Betriebs hydraulisch abgekippt und neu bestückt werden.
Der feststehende Grundrahmen verfügt über eine angetriebene Drehvorrichtung. Der Karussellrahmen ist mit einer integrierten Hydraulik und Kippzylindern ausgestattet. Der Haspel wird entweder mittels eines separaten Schaltschranks betrieben oder vom Schaltschrank der Ziehmaschine mitgesteuert. Neben der oben dargestellten fundamentlosen Ausführung gibt es auch eine stärkere Ausführung, die insbesondere bei großen Durchmessern genutzt wird. Diese benötigt ein Fundament.
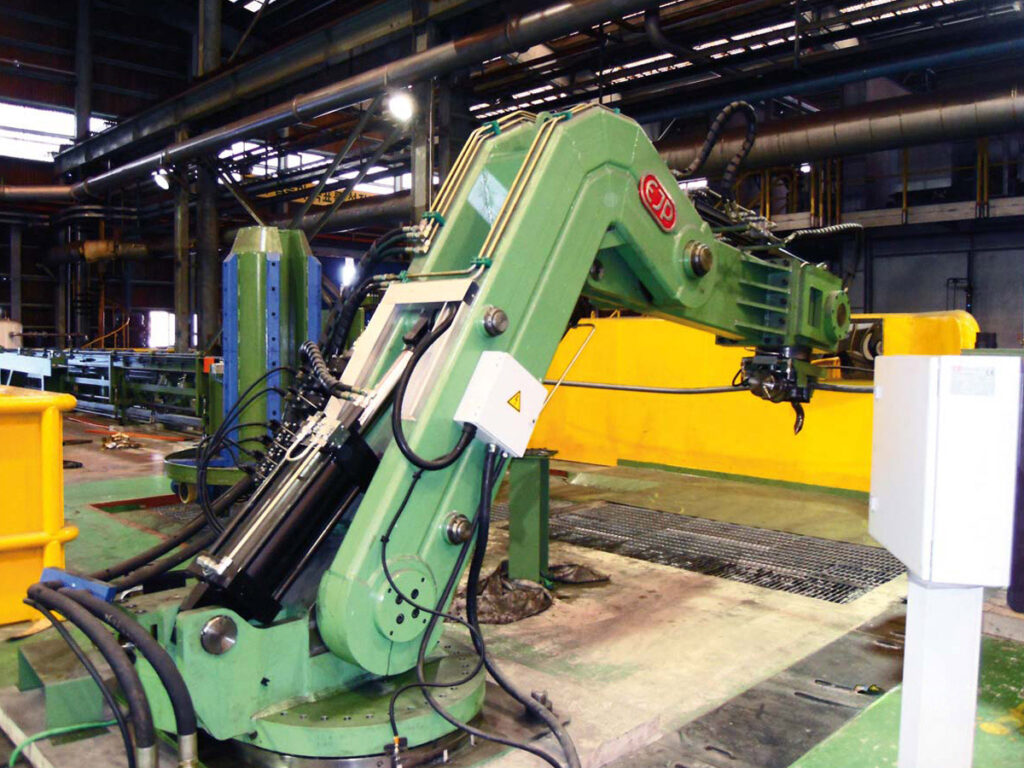
Ringaufbiegerroboter
Der Ringaufbiegerroboter führt den Ringanfang in den Vorrichter ein.
Der feststehende Grundrahmen verfügt über eine angetriebene Drehvorrichtung. Der Ringaufbiegeroboter kann vom Bediener mittels Joysticks jedwede Bewegung ausführen, so dass es möglich ist, den Drahtanfang ohne manuelles Eingreifen zu öffnen. Neben dem oben dargestellten Ringaufbiegeroboter gibt es auch noch die klassische Version „RIBI“.
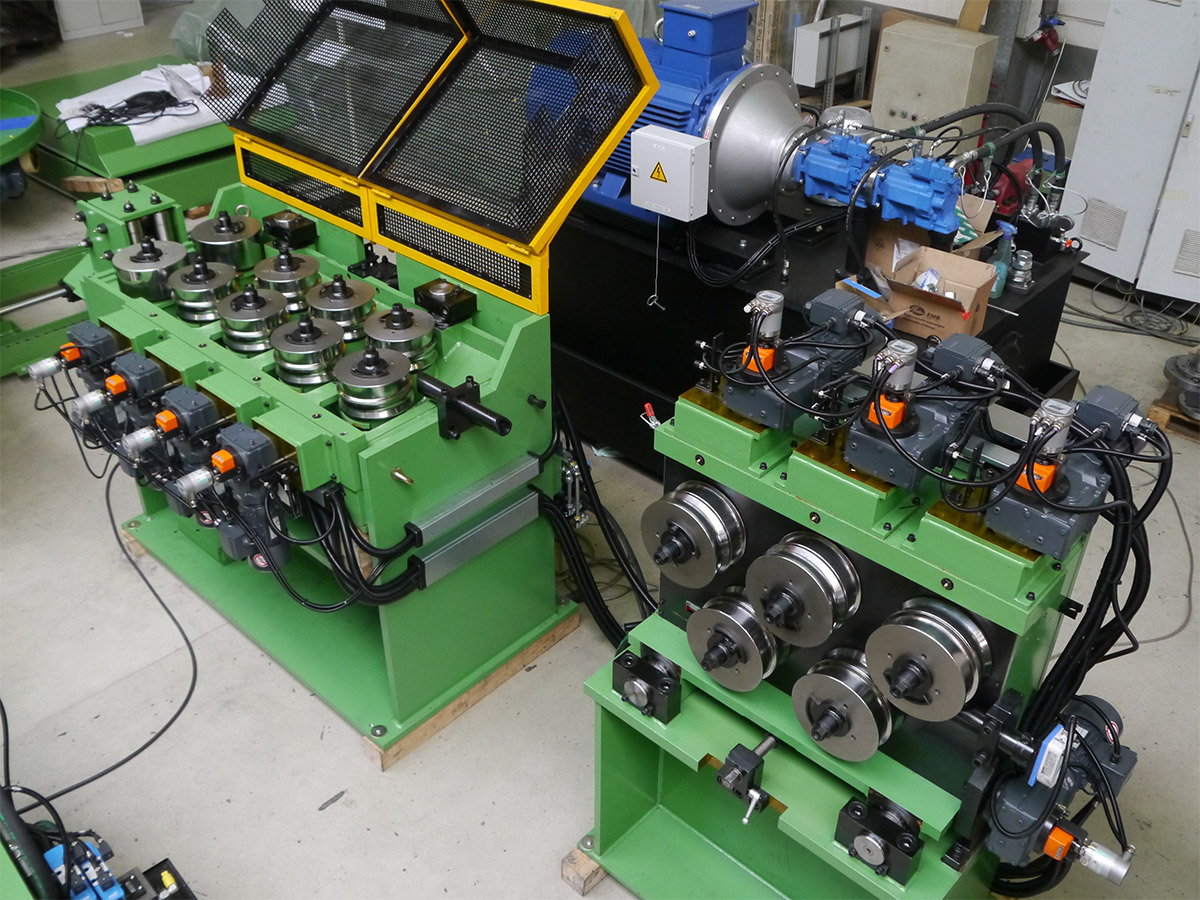
Vorrichter
Die Vorrichtmaschine sorgt für die optimale Vorbereitung auf die Folgeprozesse.
Der angetriebene waagerechte Vorrichter ist wichtig für das starke Durchbiegen entgegen der Wickelrichtung des Drahtrings. Er wird von dem senkrechten, nicht angetriebenen Vorrichter, gefolgt. Die Rolleneinstellung erfolgt, je nach Ausführung, manuell oder motorisch, wird aber stets digital angezeigt. Um ein schnelles Umrüsten der Maschinen zu ermöglichen, verfügt die Vorrichtmaschine über doppelte Rollen je Welle, so dass ein Wechsel der Rollen unnötig wird.
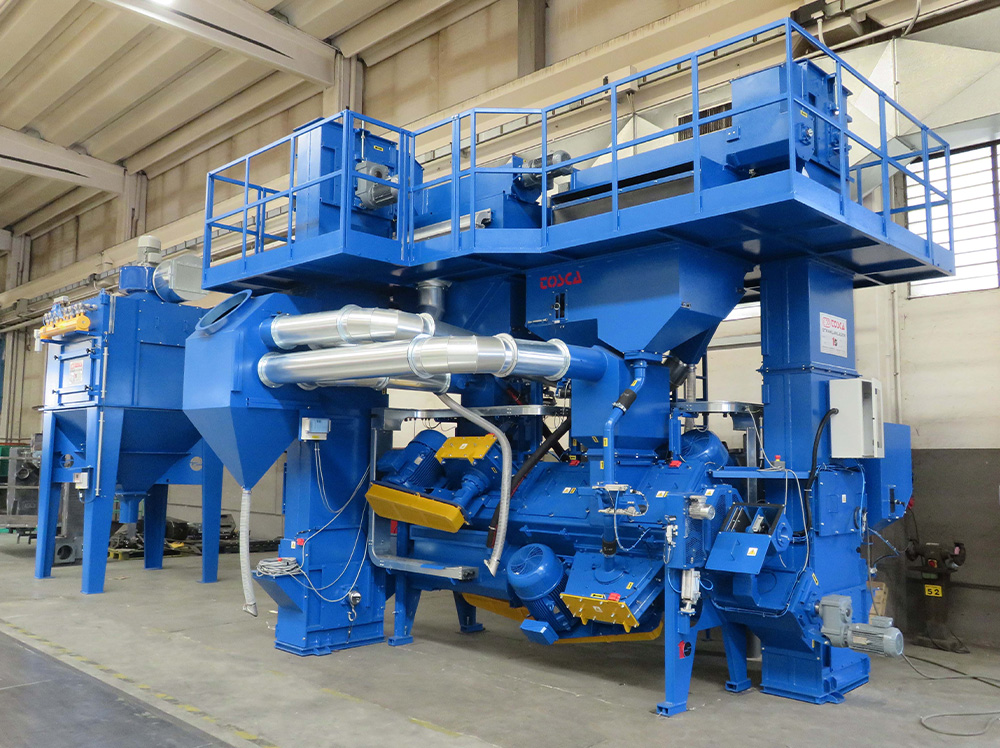
Strahlanlage
Die Strahlanlage bringt die Oberfläche des Ausgangsmaterials in den optimalen Zustand.
Bei der Bearbeitung von Stahl und Stahllegierungen wird das Material vor dem Ziehen durch eine Schleuderradstrahlanlage mechanisch entzundert. Hierdurch wird gewährleistet, dass nur metallisch reines Material in den Ziehstein der Ziehmaschine gelangt.

Einstoßvorrichtung
Die Einstoßvorrichtung sorgt für die präzise Zuführung in die Zieheinheit.
Das direkte Einstoßen des Ringanfangs in den Ziehstein kann, je nach Material und Dimension, den Anspitzvorgang ersetzen. Die Einstoßkraft kann bis zu 920 kN betragen. Die gleichzeitige motorische Verstellung des Ziehsteinhalters sorgt für die optimale Ausrichtung des Ziehsteins. Ein großer Öffnungshub verhindert eine Beschädigung durch die Einstoßbacken während des Ziehprozesses.
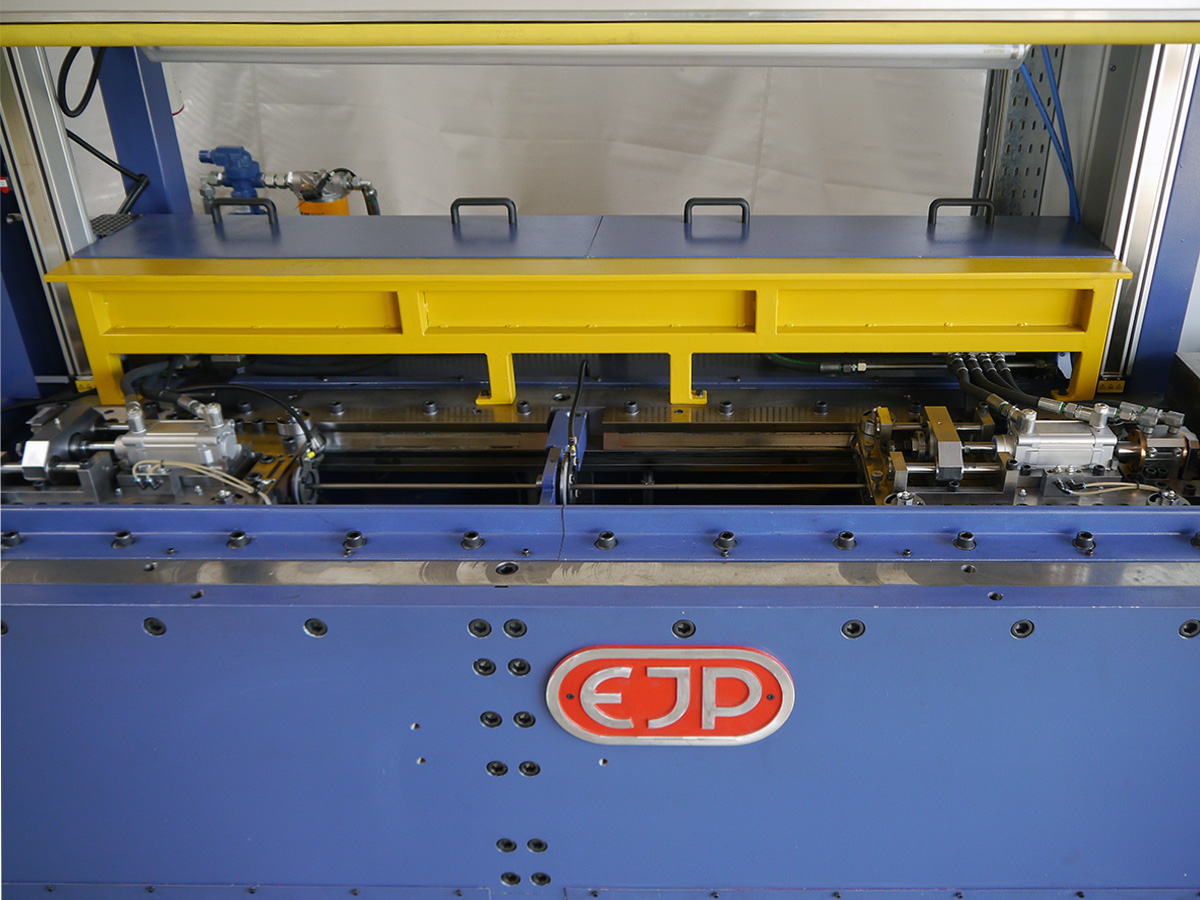
Zieheinheit
Die konventionelle Zieheinheit besteht aus zwei Ziehschlitten, die über Kurven angetrieben werden.
Durch dieses von Schumag seinerzeit entwickelten Ziehverfahrens ist es möglich, Material im Geradeaus-Verfahren zu bearbeiten. Die von uns weiterentwickelten Zieheinheiten zeichnen sich durch rollengeführte Ziehschlitten, Ziehkurven aus geschmiedetem Material und einer elektronisch gesteuerten, servoelektrischen oder hydraulischen Ziehbackensteuerung aus. Es werden Geschwindigkeiten bis zu 150 m/min und Ziehkräfte bis 460 kN erzielt.
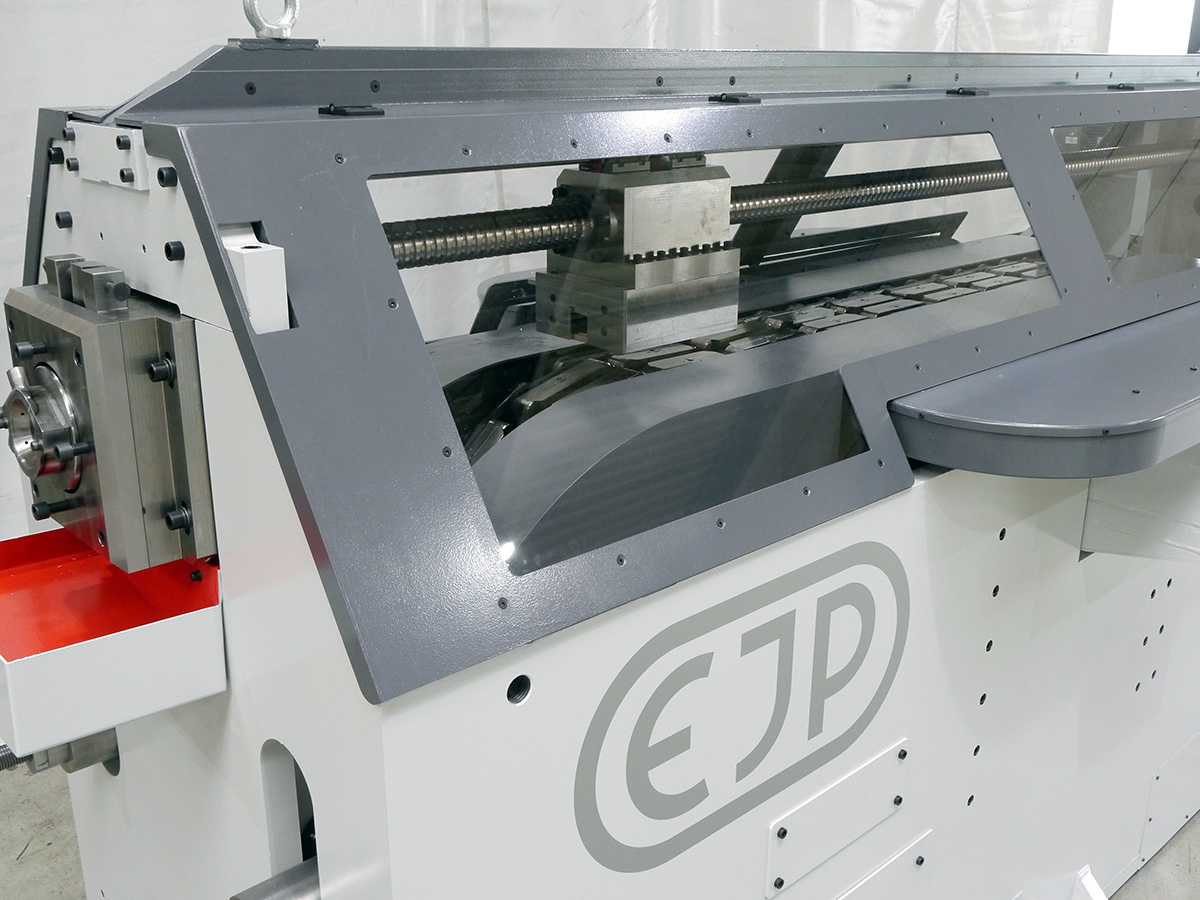
Raupenzug
Der Raupenzug ist eine Ziehmaschine der neueren Generation. Sie besteht aus zwei Ketten, die für höhere Ziehgeschwindigkeiten sorgen können, als die Ziehschlittenmethodik.
Hierbei sind Ziehgeschwindigkeiten von bis zu 300 m/min erzielbar. Diese sind insbesondere bei größeren Losgrößen sinnvoll. Je nach Anwendung liegen die üblichen Geschwindigkeiten zwischen 150 und 300 m/min.
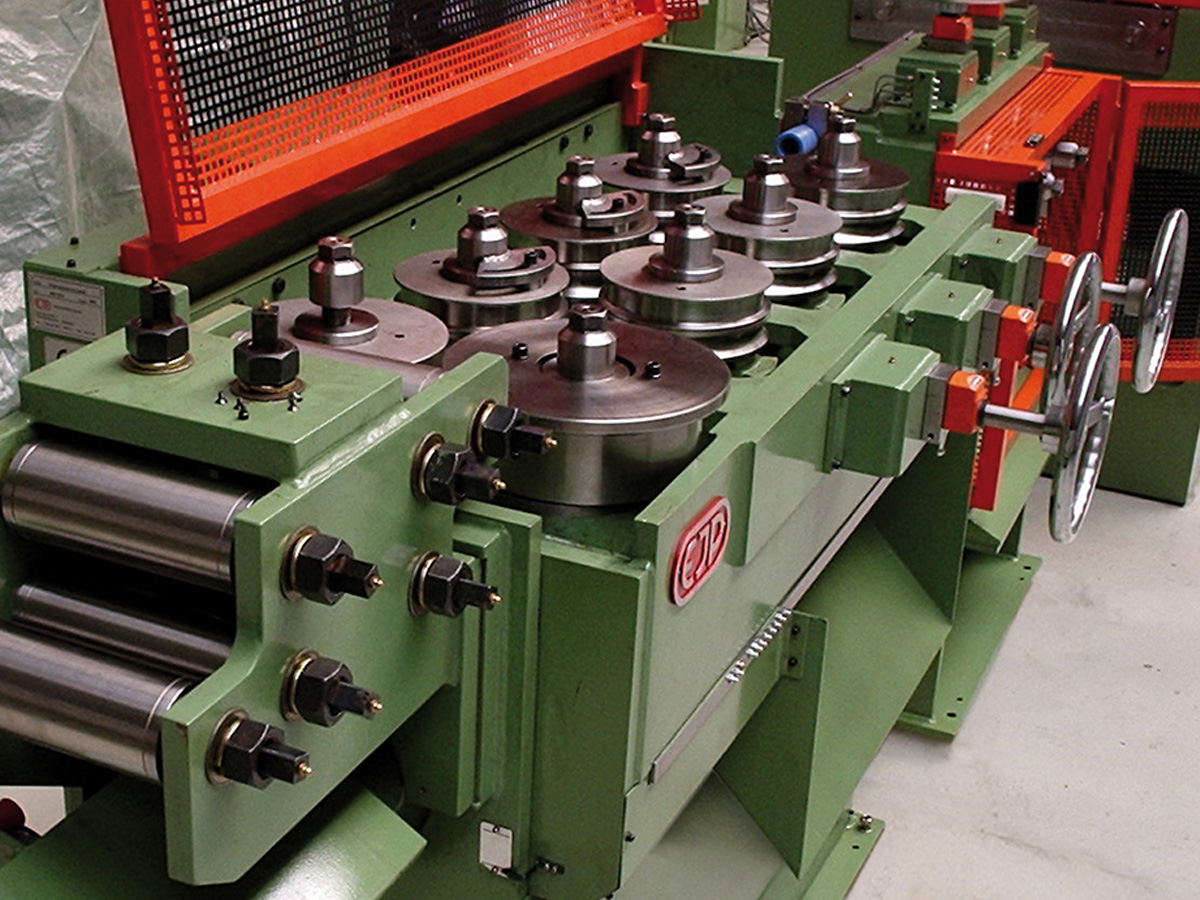
Profilrichter
Der Profilrichter sorgt für das Richten des Profilmaterials innerhalb der Ziehanlage in waagerechter und senkrechter Ebene.
Die Einheit ist mit je 7 oder 9 Richtrollen ausgestattet, die manuell oder motorisch eingestellt werden können. Ihre Position wird stets digital angezeigt. Um ein schnelles Umrüsten der Maschinen zu ermöglichen, verfügt der Profilrichter über doppelte Rollen je Welle, so dass ein Wechsel der Rollen unnötig wird.
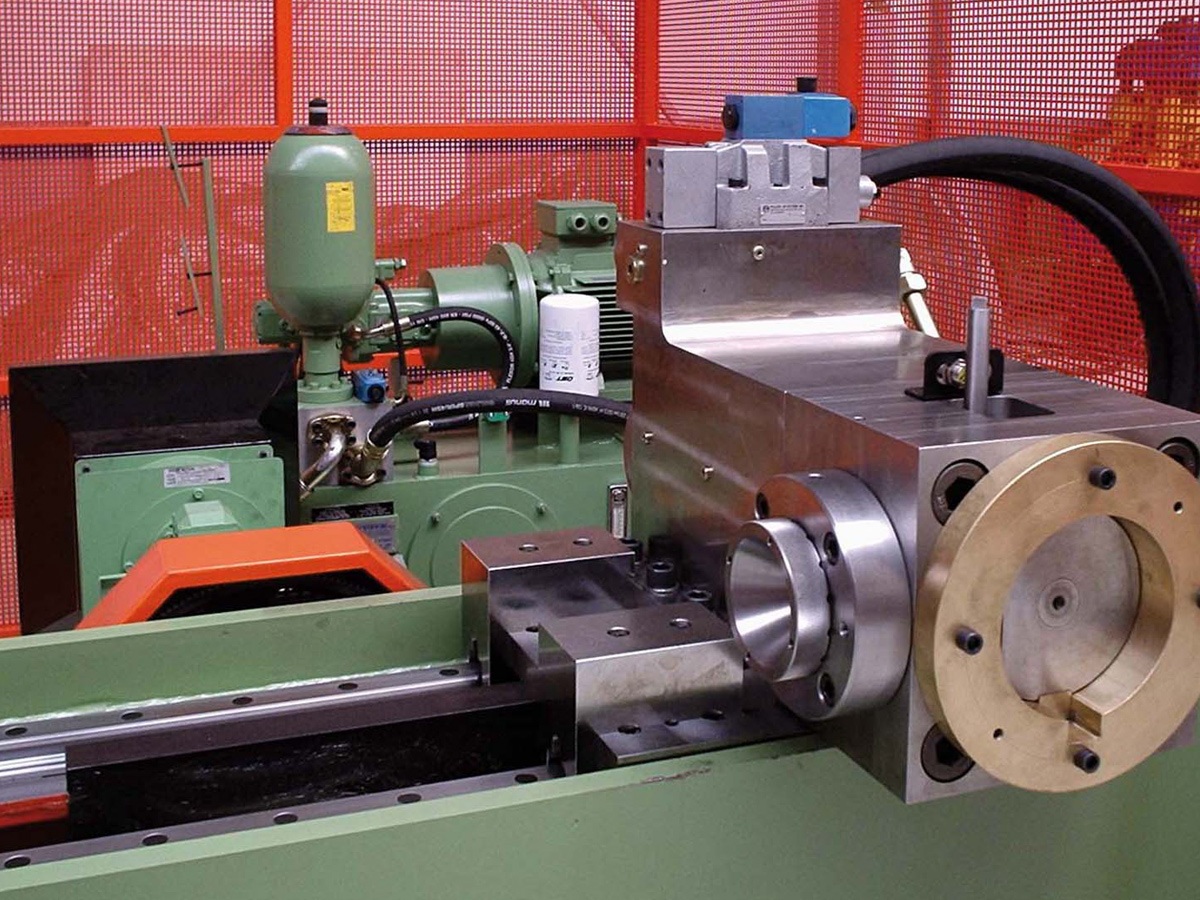
Hydraulische Schlagschere
Die hydraulische Schlagschere trennt das Material fliegend, mit zwei Scherbüchsen.
Der elektrische Servoantrieb ermöglicht eine präzise Geschwindigkeitssteuerung des Scherenschlittens. Die hohe Trenngeschwindigkeit und die feine Justage der Scherbüchsen ermöglichen optimale Schnittflächen. Der Schnitt ist auch im Standbetrieb möglich. Eine Restendensteuerung kann zusätzlich eingesetzt werden. Wenn keine Schere eingesetzt werden kann (Rohre, Hohlprofile etc.), wird anstelle des Scherenkopfes eine Sägeeinheit oder eine spanlose Trennvorrichtung auf dem Grundgestell montiert.
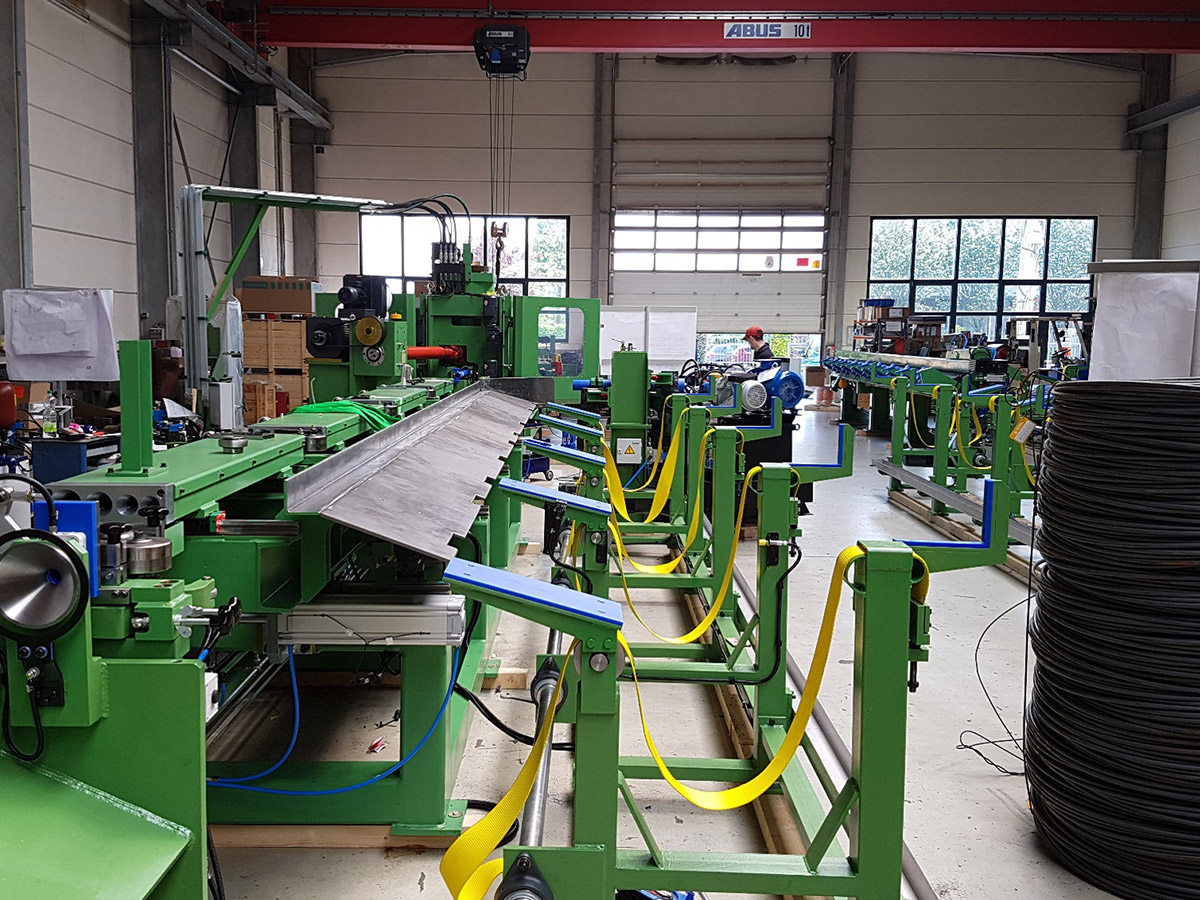
Rohrführung
Die schallisolierte Kastenrohrführung ist manuell oder motorisch quer verfahrbar.
Sie gewährleistet durch verschiedene
Rohrdurchmesser eine enge Führung der Stäbe zur nächsten Anlageneinheit. Bei Bedarf kann die Rohrführung mit einem seitlichen Auswurf sowie Transporteinheiten ergänzt werden.
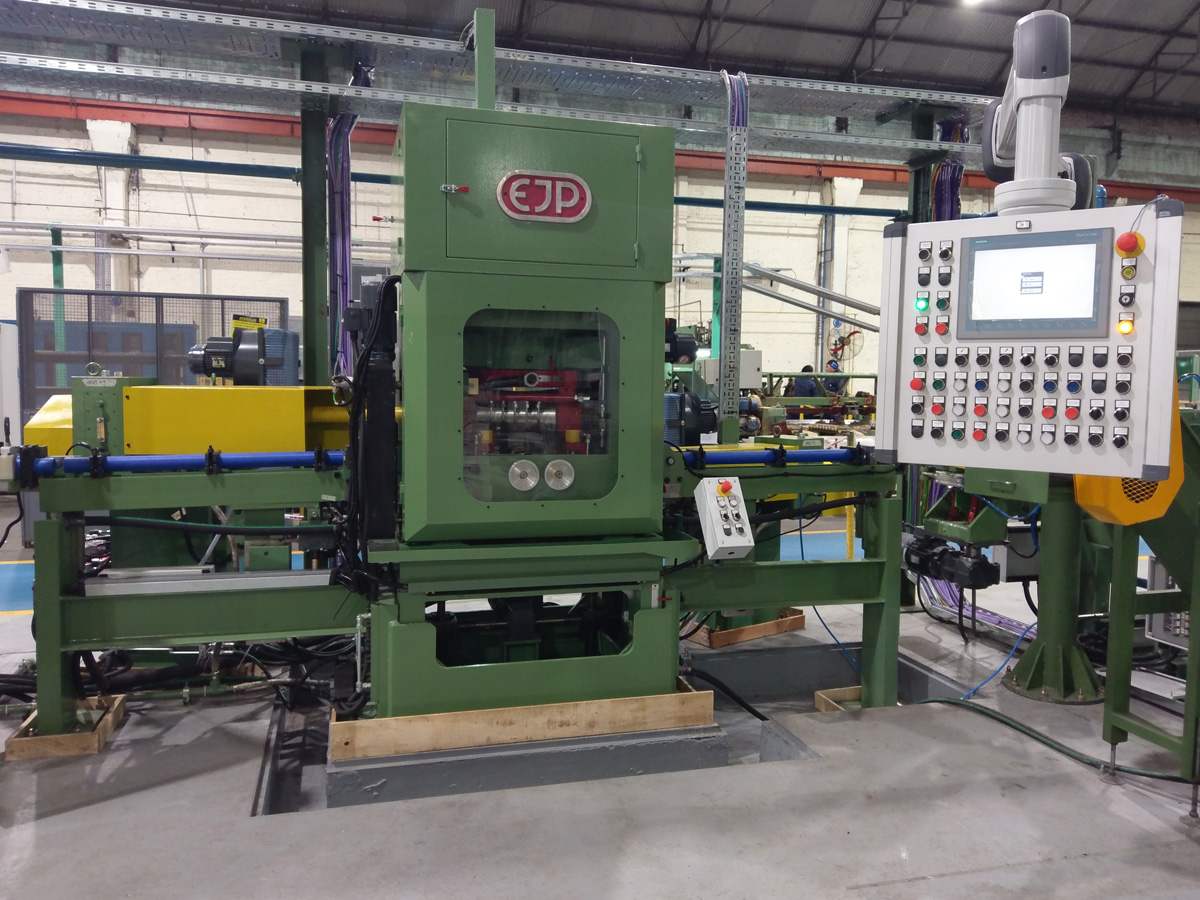
2-Walzen-Richtmaschine
Die 2-Walzen-Richtmaschine sorgt für eine präzise Geradheit bei gleichzeitig hoher Oberflächengüte.
Die höhenverstellbaren 2-Walzen-Richtmaschinen verfügen über eine feste Unterwalze und eine verstellbare Oberwalze. Die Verstellungen werden motorisch ausgeführt. Die verstellbaren Komponenten werden hydraulisch geklemmt. Alle Parameter-Einstellungen werden auf Kundenwunsch mittels HMI-System gespeichert und stehen beim Einrichten der Maschine zur Verfügung.
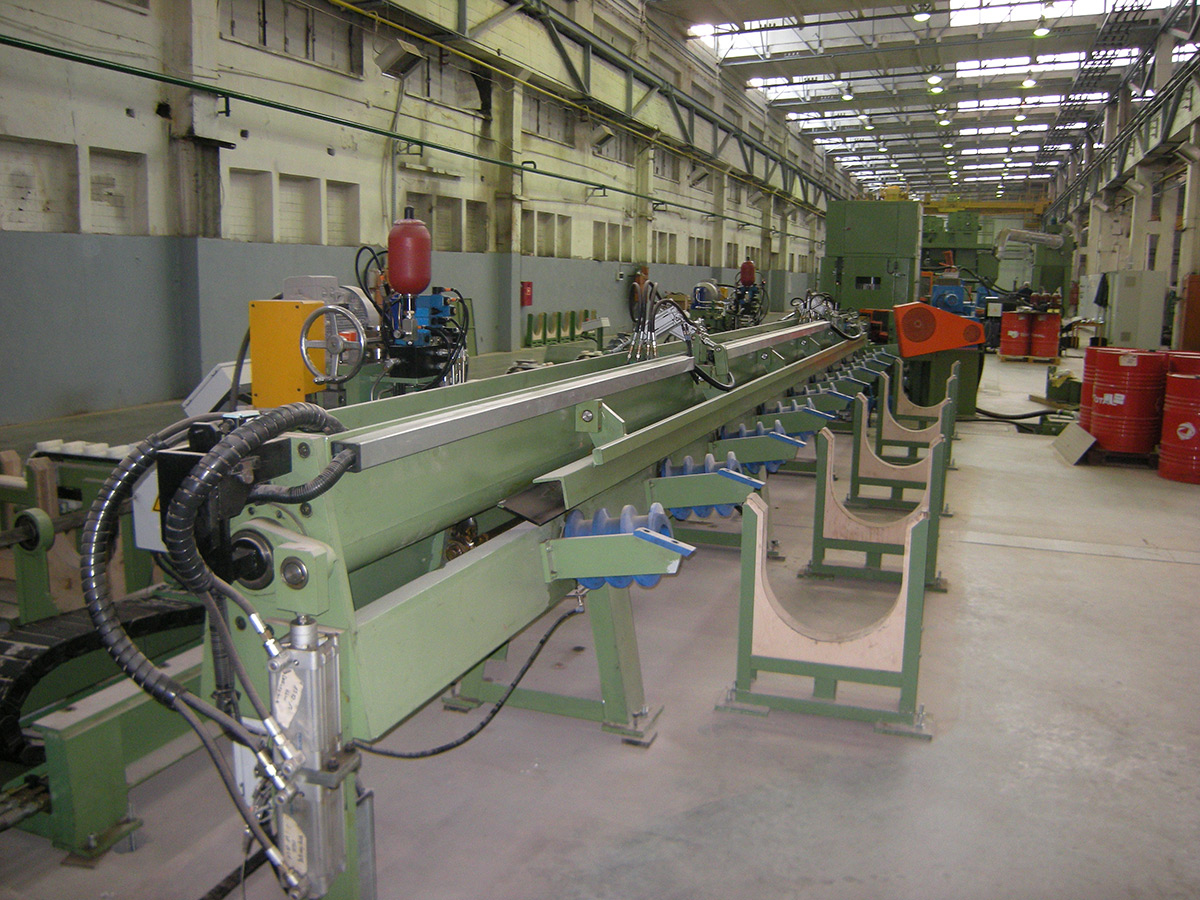
Beidseitige Ablage
Am Ende der Ziehlinie ist eine beidseitige Ablage zum
wechselseitigen Ablegen der Stäbe angeordnet.
Je nach Einsatz von Prüfanlagen in der Ziehlinie werden die als defekt klassifizierten Stäbe von der beidseitigen Ablage auf der rückwärtigen Seite ausgeworfen. Die als gut befundenen Stäbe werden auf der Vorderseite ausgeworfen. Das Schneckensystem sorgt für eine präzise und störungsfreie Ausrichtung, bevor die Stäbe in die nachfolgende Anfasmaschine, andere Maschineneinheiten oder die Sammelmulde gelangen.
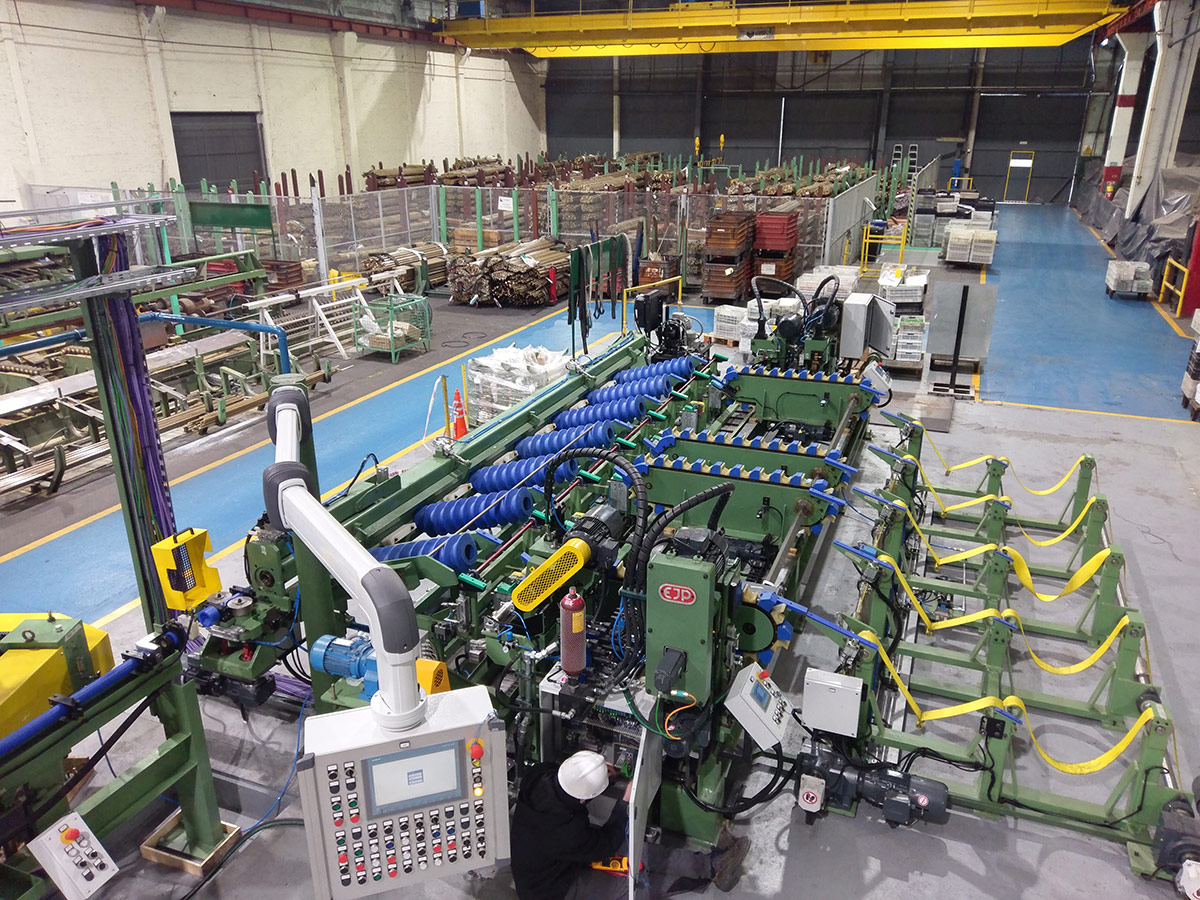
Anfasmaschine
Das Stabmaterial benötigt oftmals eine bestimmte Form des Stabendes für die weitere Verarbeitung.
Die Anfasmaschine hat die Aufgabe, die Stabenden nach Vorgabe zu bearbeiten. Hierzu gehören das Anfasen, Planen oder Fräsen der Stabenden. Insbesondere im Buntmetallbereich ist dem Fasprozess noch ein Sägeprozess vorgelagert. Je nach Stablänge und Durchmessern kann das Stabtransportsystem innerhalb der Anfasmaschine als Kettentransport oder als Hubbalken ausgeführt sein.
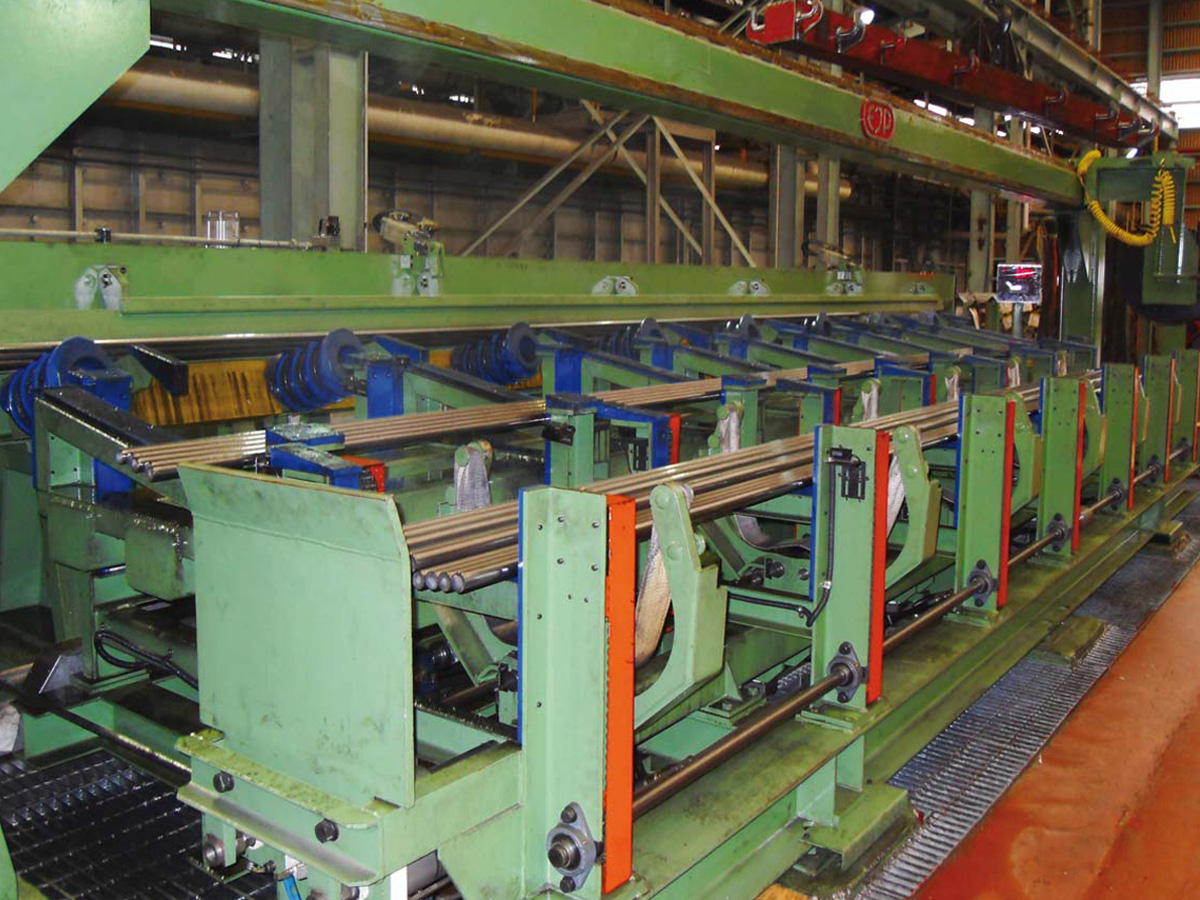
Doppelte leise Mulde
Die Mulde sorgt für ein gedämpftes Sammeln (Auffangen) des Materials.
Die Geräuschreduzierung ist mit einer schonenden Sammlung des Endmaterials verbunden. Durch den Einsatz einer doppelten Mulde, bestehend aus Zwischenpuffer und Fertigmulde, ist es möglich, ein Stangenbund während laufender Produktion abzubinden und zu entnehmen.
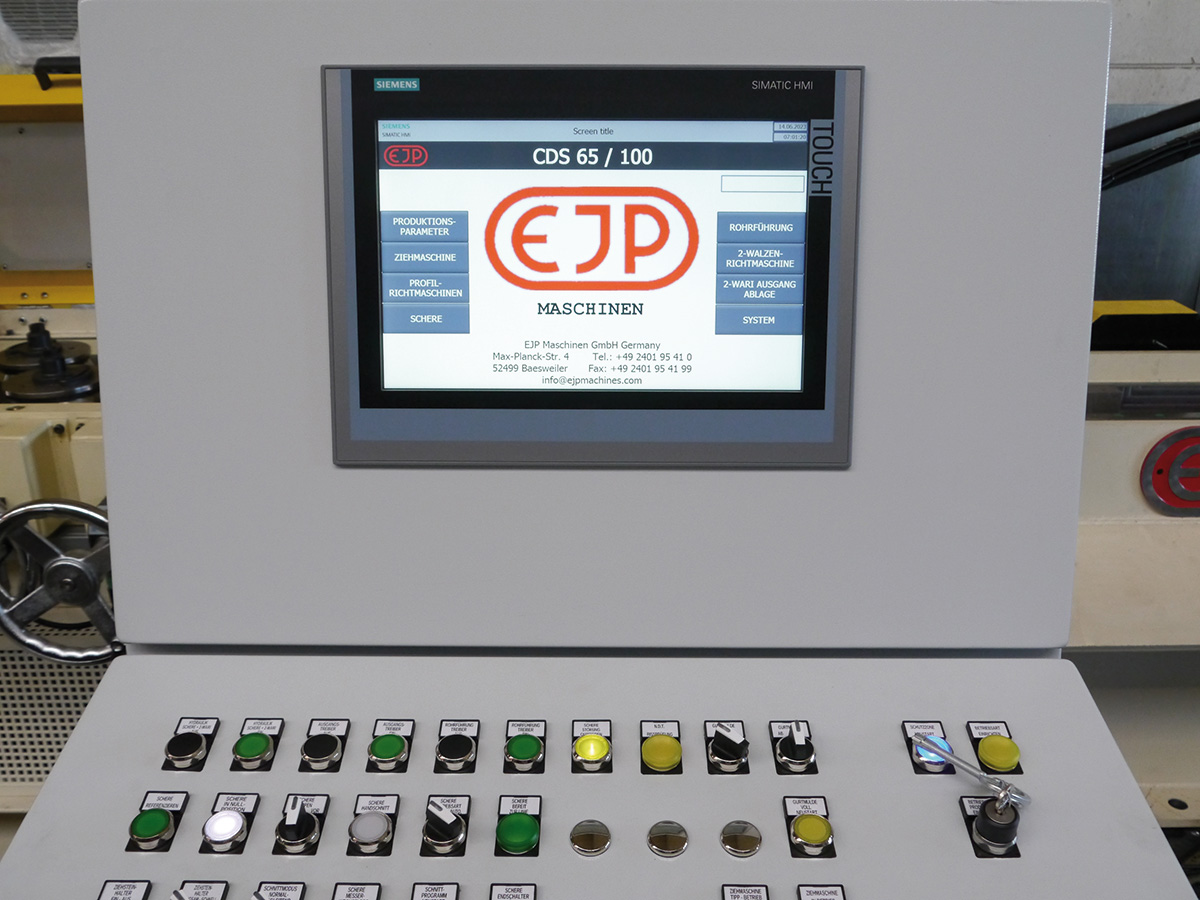
Elektrische Steuerung
Die Gesamtanlage wird mit Hilfe einer modernen elektrischen Steuerung kontrolliert und betrieben.
Jeder Prozessparameter wird erfasst und bei Bedarf dem Bediener, dem Wartungspersonal und der Fertigungsleitung zur Verfügung gestellt. Die elektrische Steuerung basiert auf marktgängigen Standardkomponenten von SIEMENS oder anderen namhaften Herstellern nach Kundenwunsch. Mittels einer internetbasierten Fernwartung ist es möglich, bei Störfällen umgehende Soforthilfe zu gewähren. Die Gesamtsteuerung ist Industrie 4.0 geeignet.
Kontakt aufnehmen, ganz einfach.
Ihr Ansprechpartner

Geschäftsführer EJP