Schälanlagen

PM-Baureihe
Die PM-Baureihe basiert auf den neuesten Entwicklungen und verfügt über den einzigartigen, patentierten PM Schälkopf.
Im Gegensatz zu allen Wettbewerbsanlagen erfolgt die PM-Schälkopfverstellung rotativ und ermöglicht somit eine maximale Stabilität, unabhängig vom bearbeiteten Durchmesser. Bei der PM-Baureihe erfolgt die Kompensation des Schneidplattenverschleisses automatisch. Hierzu wird ein Lasermesssystem eingesetzt.
Die Systemkomponenten
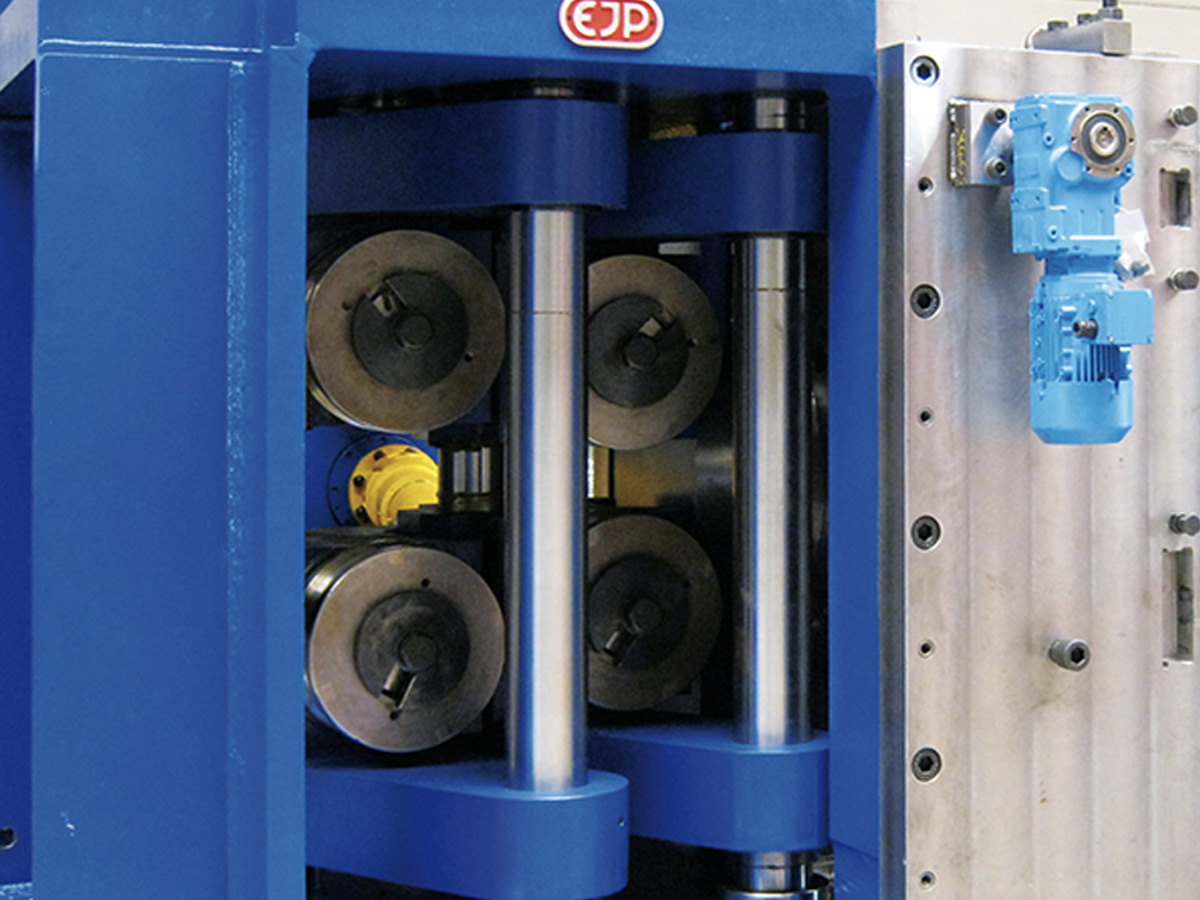
Einschub-Apparat
Der Einschubapparat besteht aus vier groß dimensionierten Rollen, angetrieben von Servomotoren.
Der Antrieb erfolgt direkt oder über Verteilergetriebe. Hierdurch ergibt sich eine präzise Synchronisation des Materialvorschubs mit dem Auszugswagen. Dieser ist ebenfalls über einen Servomotor angetrieben. Hydraulikzylinder mit Servoventilen sorgen für präzises und kräftiges Halten des zu schälenden Materials. Der Hydraulikdruck kann vom Bedienpult aus eingestellt werden und wird in der Rezeptsteuerung hinterlegt. Eine leichte Zugänglichkeit zu den Rollen für schnelles Wechseln ist gegeben.
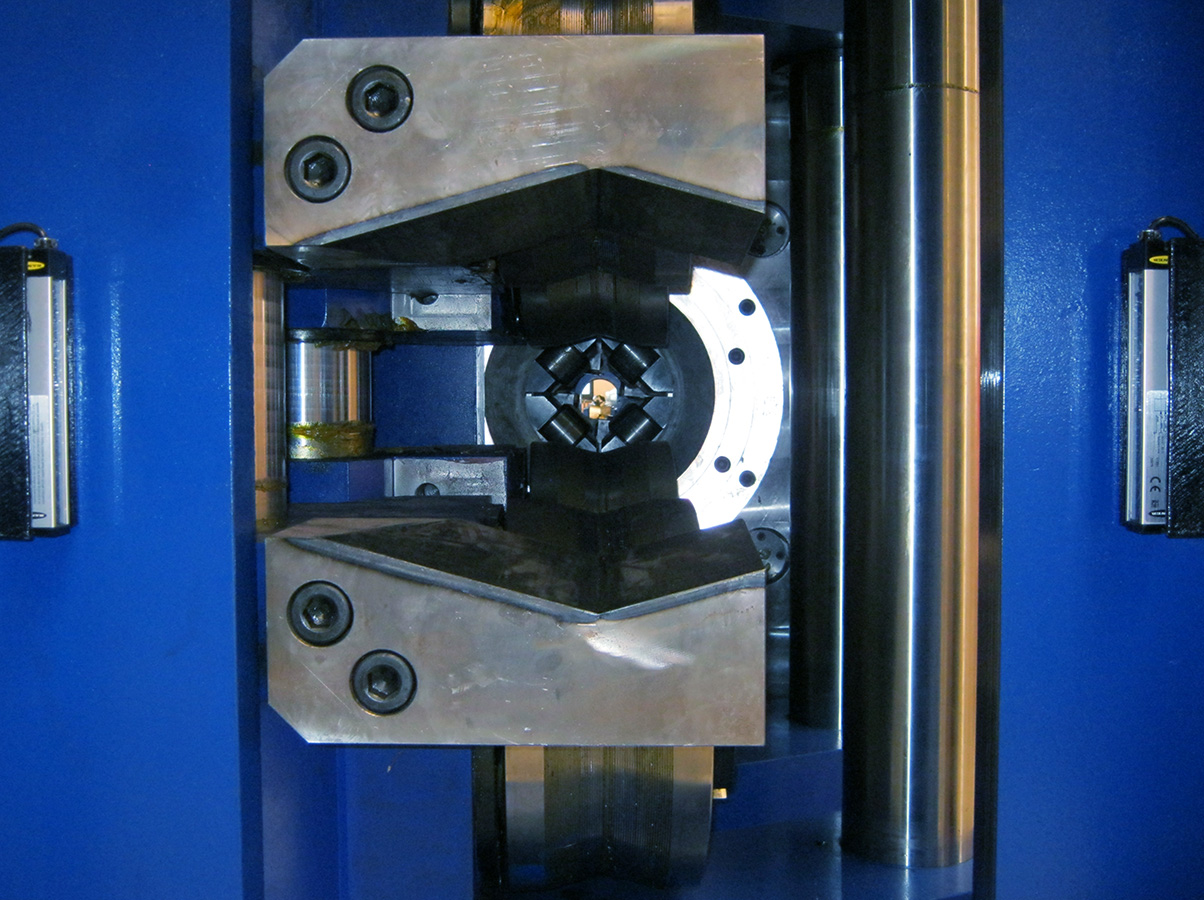
Einlaufführung
Die Einlaufführung ist ein stabiles Führungssystem für die präzise Zuführung des Schwarzmaterials zum Schälkopf.
Die Rollen sind aus Werkzeugstahl zur Erzielung einer langen Lebensdauer. Die Einlaufführung verfügt über Tellerfedereinheiten zum Ausgleich von Durchmesserschwankungen sowie Unrundheit des Ausgangsmaterials. Die konzentrische Verstellung der Einlaufführung erfolgt durch Handrad oder Stellmotor.
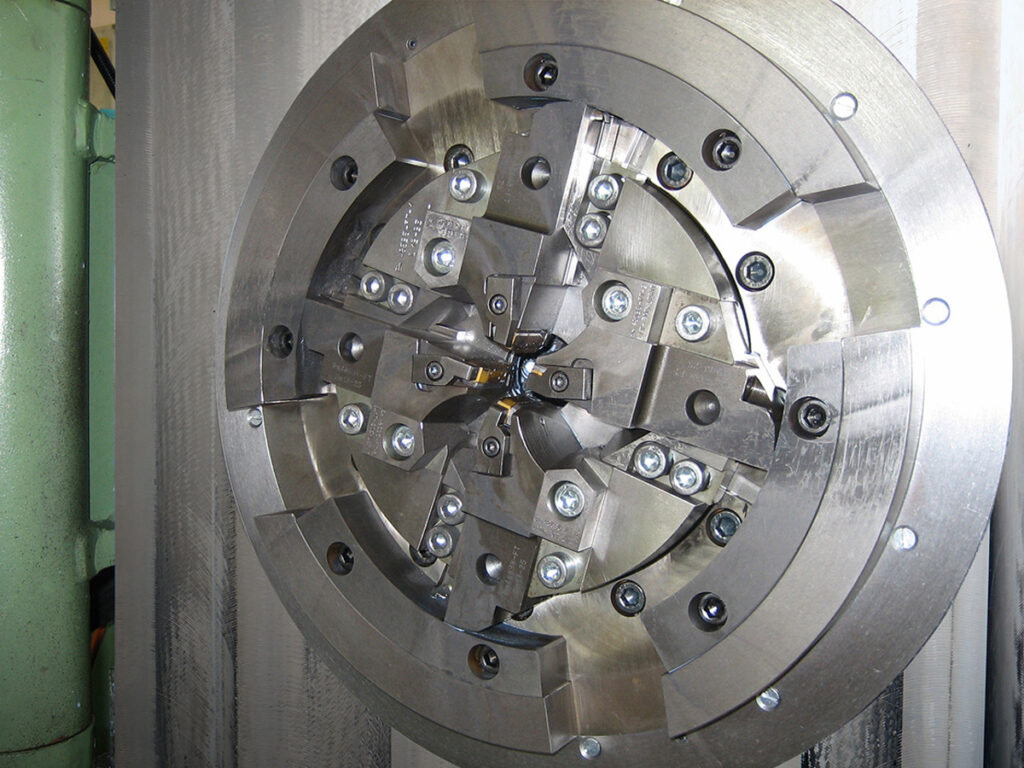
Schälkopf mit Antrieb und Verstellung
Der Schälkopf verfügt über eine Verstellung, die durch die Rotation des Innenrings erfolgt.
Hierdurch wird eine einzigartige Stabilität der Werkzeughalter erzielt. Diese bilden mit den montierten Wendeschneidplatten, gemeinsam mit dem Außenring des Schälkopfes und dem Maschinengehäuse eine Linie. Hierdurch werden die sonst üblichen Mikrovibrationen verhindert. Es wird eine absolute Konzentrizität aller vier Werkzeughalter durch Verzicht auf mechanische Verstellelemente am Schälkopf erreicht. Der Antrieb des Schälkopfes erfolgt durch ein Hochleistungsgetriebe. Es wird durch einen Servomotor angetrieben.
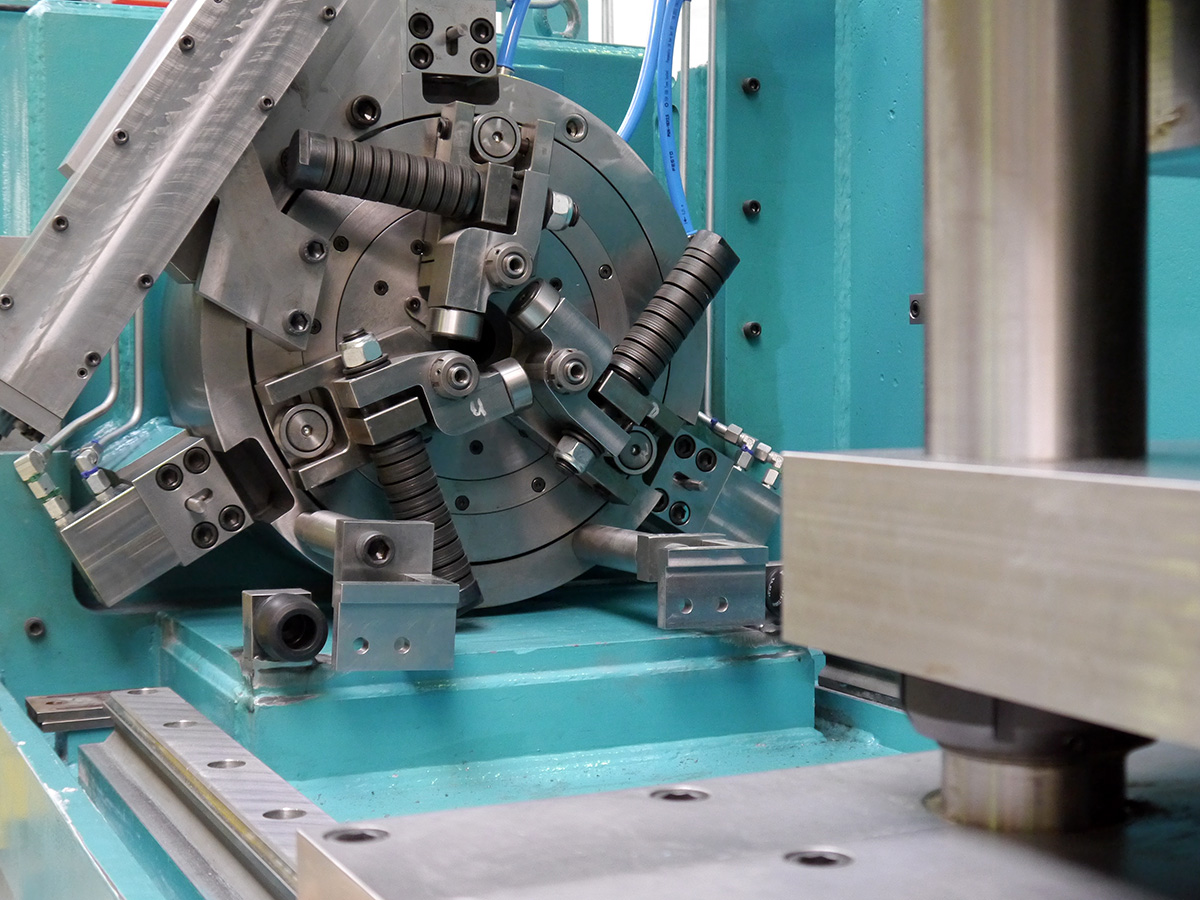
Auslaufführung
Die Auslaufführung dient der präzisen Führung des geschälten Materials nach dem Schälkopf.
Sie verfügt über eine zweifache Materialführung. Das geschälte Material wird direkt nach dem Schälkopf durch muschelförmige Gleitschuhe aus Messingbronze geführt. Anschließend wird es von Rollen aus Werkzeugstahl gehalten, bevor es die Auslaufführung verlässt. Die konzentrische Verstellung der Auslaufführung erfolgt durch Handrad oder Stellmotor.
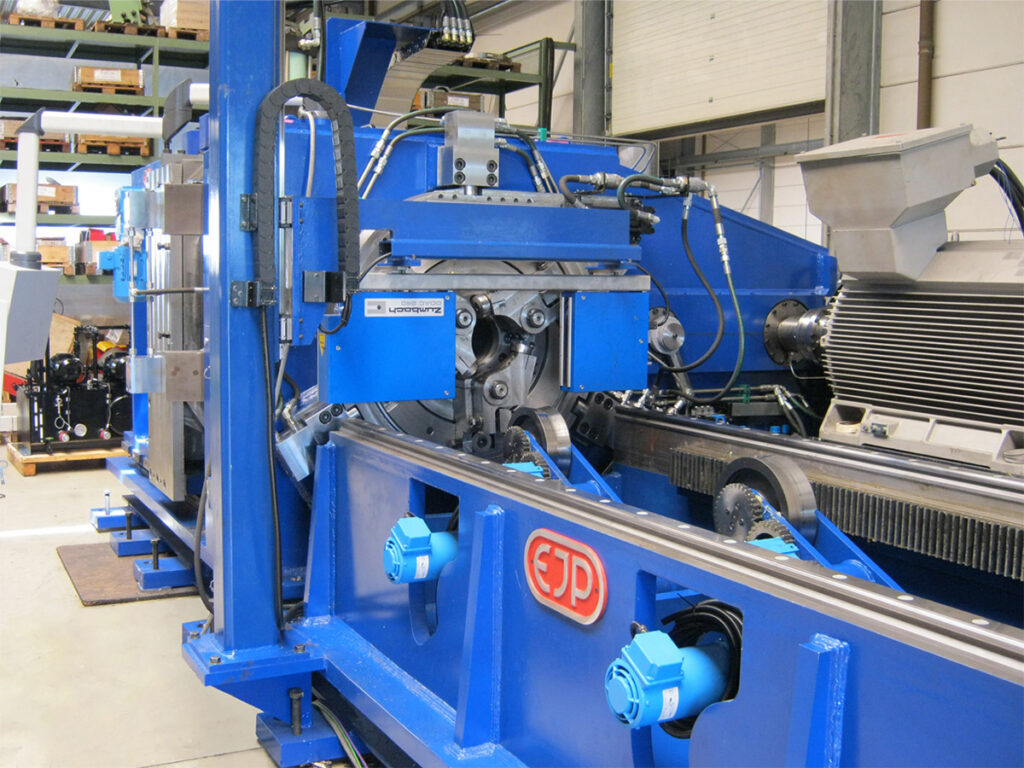
Lasersystem
Unsere Schälmaschinen verfügen über ein hochpräzises Lasermesssystem zur permanenten Überwachung des erzielten Schälergebnisses.
Bei PM Schälanlagen erfolgt eine automatische Kompensation des auftretenden Werkzeugverschleißes. Hierdurch wird sichergestellt, dass die gewünschte voreingestellte Produkttoleranz bis zum Austausch der Wendeschneidplatten eingehalten wird. Bei HS Schälanlagen erfolgt die Kompensation des auftretenden Werkzeugverschleißes durch manuelle Verstellung.
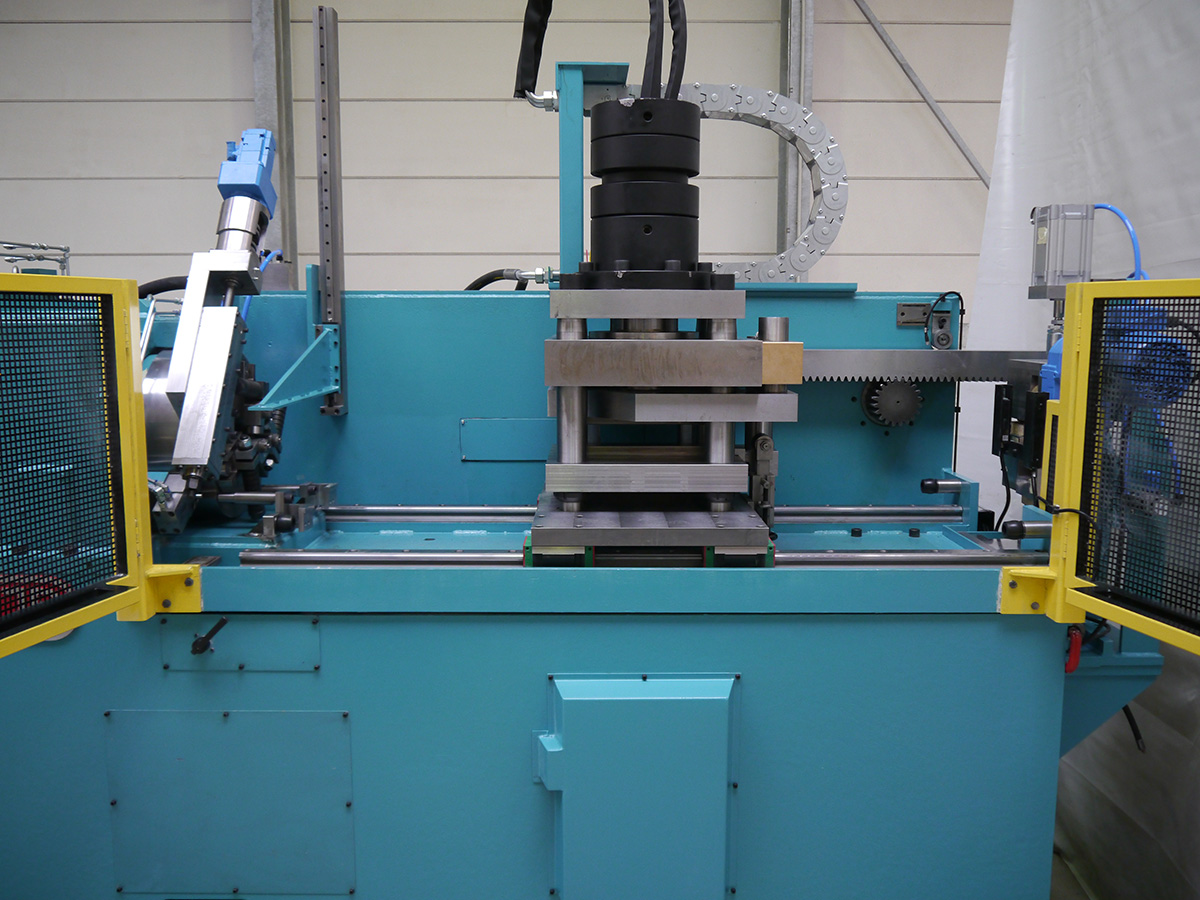
Auszugswagen
Der Auszugswagen verfügt über Hydraulikzylinder mit Servoventil für präzises und kräftiges Halten des geschälten Materials.
Der Hydraulikdruck kann vom Bedienpult aus eingestellt werden und wird in der Rezeptsteuerung hinterlegt. Klemmbacken aus poliertem Werkzeugstahl sorgen für beschädigungsfreies Klemmen des geschälten Materials. Der Antrieb erfolgt durch einen Servomotor. Hierdurch wird eine präzise Synchronisation des Materialtransports mit dem Einschubapparat ermöglicht, welcher ebenfalls über Servomotoren angetrieben wird.
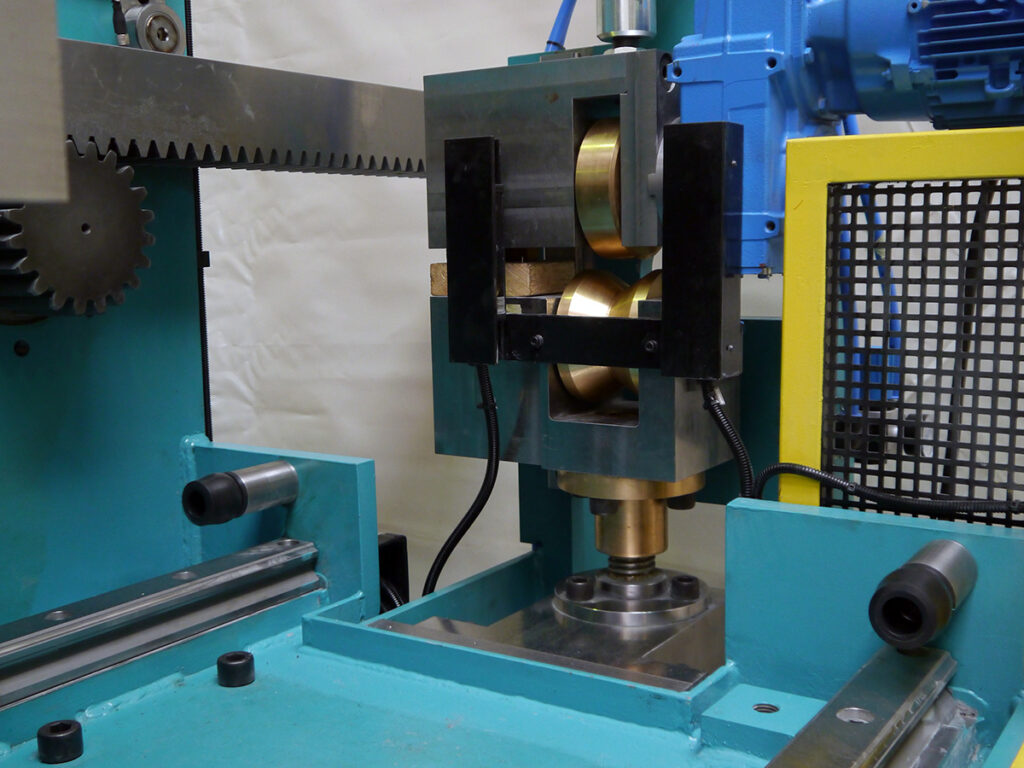
Ausgangstransportapparat
Der Ausgangstransportapparat besteht aus zwei Präzisionsrollen, von denen eine Rolle angetrieben ist.
Sobald ein Stab die Auslaufführung verlassen hat, wird dieser vom Ausgangstransportapparat übernommen. Die Aufgabe des Ausgangstransportapparats besteht darin, den Stab zum Auslaufrollgang zu transportieren.
Kontakt aufnehmen, ganz einfach.
Ihr Ansprechpartner

Geschäftsführer EJP